Inconsistent cases: Case forming annoyances, and how to overcome them
Published January 5, 2021
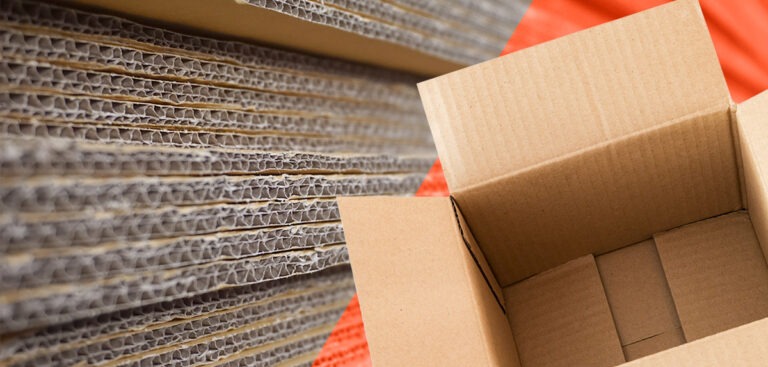
A jammed case erector and skewed corners are two of the biggest annoyances when it comes to case forming. When it happens with any frequency, it creates an unwanted disruption to your production line.
Sometimes, it can be difficult to tell if the problem comes down to materials or mechanics. Use this troubleshooting guide to help you get to the root cause of your jammed case erector and skewed boxes.
How cardboard quality can lead to jammed machines
A well-constructed case always starts with clean, dry corrugated cardboard. When cardboard is dirty or damp, the case erector will have trouble opening as well as sealing the cases. If your machine gets jammed, consider examining your cases’ cardboard quality as your first point of trouble-shooting.
- If the case erector uses the opposing cup function, the presence of dust on the cardboard’s surface can cause interference. In this situation, the equipment may have trouble opening the case, which can lead to stoppage.
- Damp cases are more likely to tear, especially when the machine uses the pin and dome opening method.
- Dirty and damp surfaces can also prevent tape and glue from bonding with the cardboard. Although this issue doesn’t necessarily lead to jammed equipment, it’s worth noting that it can increase the risk of cases opening unexpectedly during handling, which can result in product damage or — worse — possible injury to personnel.
Checking for good cardboard conditions is important. Sometimes quality issues can be resolved by your supplier. If your cardboard stock arrives dusty, for example, the dust could be a byproduct of manufacturing the cardboard blanks. Whether you contact your supplier or resolve the issue on site, correcting quality issues could prevent equipment jams and save you time, cost and other potential damages.
Skewed corners: Is it mechanical or material?
When it’s time to palletize the load for shipment, straight, squared corners are critical to building that sturdy stack.
When building a pallet, boxes are stacked and interlocked to form one sturdy, singular block. Your boxes are designed to take on a certain amount of load and pressure, but something as simple as a crooked corner can affect the compression strength. Why is this problematic? Too many skewed corners will weaken support, making your stacks unstable and more likely to shift or even topple in transit. This problem can exist even if the pallet is secured in shrink-wrapping. Skewed corners can result in damaged inventory, not to mention higher risk of injury to personnel.
If your boxes have skewed corners, check to see if the problem comes from the cardboard material itself. If the cardboard passes inspection, then some issue with your packaging and palletizing equipment could be the cause.
When material tolerance causes skewed corners
Like many manufactured materials, corrugated cardboard blanks have minor, imperceptible variations. The variations that occur during manufacturing of the case blanks are known as material tolerance.
As long as the material tolerance falls within a specific range, the constructed case should be sound. However, if the joints of the cardboard case are not glued properly, the end result is skewed corners and a misshapen case.
These out-of-tolerance cases can sneak up during a production run, so it’s good practice to have your team spot-check the formed cases throughout all phases of packaging. If two of four corners are skewed, the cause is likely coming from an out of range material tolerance.
Once you identify problematic batches of cases that are outside of the tolerance, you can pull the bad blanks from the run and contact your supplier to resolve the issue.
Mechanical solutions to skewed corners
If all four corners are skewed, with two being greater than 90 degrees and the remaining two less than 90 degrees, then the issue lies with case assembly.
A well-designed case erector is one effective way to solve the problem. Investing in a machine that uses smart features to check and correct skewed cases is your best bet. INSITE’s Case Erector has an active box-squaring feature that can ensure squared corners, even after a changeover. Here’s how it works:
- A photo eye scans the leading edge of the case, measuring the corner’s angle
- If the corner is not 90 degrees, one of the side belts that guides the casebox responds with a burst of speed to get it into alignment, which adjusts the squaring
- The box rolls off, ready for packing, with corrected, even corners
[For a closer look at how active box squaring works, read Hip to be square: The benefits of active case squaring]
When it comes to your production, forming cases should be the least of your concerns. Ideally, this segment of secondary packaging should reach a production level that is truly automated and practically invisible. If your endgame includes fewer machine jams and higher repeatability, it might be time to invest in a new case erecter.
Consider contacting an INSITE product specialist to start solving those equipment jams and case forming issues.